Research - (2019) Volume 7, Issue 6
Analysis of Nd: YAG Laser (1064 and 532 nm) Interaction with Zirconia Dental Implant after Different Exposure Time
Sena Raed Muhy and Basima Mohammed Ali Hussein*
*Correspondence: Basima Mohammed Ali Hussein, Institute of Laser for Postgraduate Studies, University of Baghdad, Iraq, Email:
Abstract
Objectives: The aim of this study is to investigate the effect of Nd-YAG laser of (1064 and 532) nm wavelength in modification of zirconia implant surface roughness in order to enhance the progress of Osseo integration.
Materials and methods: Zirconia block (inCoris, Sirona) used in preparation of experimental samples. The cutting was made by CADlCAM technique. The sectioned samples were polished by using diamond paste, then sintered to get discs of (10.2) mm of diameter and thickness respectively. Q-switched Nd-YAG laser used in different parameters in this study. For (1064) nm wavelength, the used flounce was (38.22)J\cm², frequency (10) Hz and the exposure time was (3, 5 and 7) seconds in three separate trials. For (532) nm wavelength, the used flounce was (19.11)J\cm², frequency (10)Hz and the exposure time was (3, 5 and 7) second in three separate trials. All irradiated samples were assessed by scanning electron microscope and atomic force microscope for surface topography and surface roughness changes respectively.
Results: The SEM images showed increased surface porosity of irradiated samples, cracks free surfaces for both wavelengths. AFM results revealed increased surface roughness directly with exposure time for both wavelengths.
Conclusion: Q-switched Nd-YAG laser of (1064 and 532) nm wavelengths can be used for modification of zirconia implant surface.
Keywords
Dental implant, Zirconia, Osseointegration, Laser material interaction, Nd:YAG laser
Introduction
Dental implants are prosthetic units used for the replacement of missed natural roots. They inserted into the prepared bony socket to be anchored and integrated with the surrounding bone with the time, this outcome enables them to receive dental prosthesis and withstand functional loading. An intimate connection between an implant surface and surrounding bone without any fibrous tissue termed as "osseointegration".This bony connection has an important role in transferring the functional loads to the surrounding bone without stress concentrations [1].
The process of osseointegration is greatly similar to the process of bone fracture healing process except in cellular differentiation. In osseointegration, all progenitor cells are differentiated to osteoblast cells. Several points considered as basic requirements to determine if the success degree of implantation procedure. These include
A. Stability of the prosthetic unit under normal functional loads.
B. An intimate coverage of an implant surface with newly formed bone without connective tissue interruption.
C. Lack of movement between the implant unit and surrounding supporting tissue.
D. The newly formed tissue on the implant surface must be identified as a normal bone on microscopic level [2].
Bone formation process around a dental implant can be classified into contact and distant osseointegration depending on the site of bone formative cells (osteoblast cells). In the case of contact osseointegration, bone formative cells positioned on the implant surface, so the direction of newly formed bone is from implant surface toward the socket wall and vice versa in distant osseointegration [3].
The success rate of osseointegration is affected by several factors including surface roughness, surface chemistry and bulk material [4]. Cellular adhesion on implant surface considered as the main requirement for proliferation and differentiation of bone formative cells and for the stable anchorage of the implant unit with surrounding bone [5,6]. Cellular adhesion is affected by the surface roughness of the implant surface, which can enhance osteoblast proliferation, differentiation and matrix production [7]. The texture of the implant surface has an important role in tissue response against implant insertion. Rough surfaces have a larger area for anchorage with the surrounding bone, more tissue ingrowth is allowed when they compared with smooth surfaces [8,9], this clearly indicates that, implants with higher surface roughness indicated in case of poor quality and quantity of implant bed [10].
Zirconia as implant material now days considered as an alternative to titanium implant material. Because of several titanium drawback including, changes may occur on implant surface and alteration in composition and removal of oxide layer which may effect on the success rate of osseo integration. These changes may result in mucositosis, peri implantitis finally, bone destruction process ( osteolysis) which leads to implant loss [11].
Zirconia as an implant material has several mechanical properties making it a suitable alternative to widely used titanium including, high strength, hardness, corrosion resistance, and high fracture toughness [12,13]. From a biologic point of view, zirconia doesn’t exert any cytotoxic reaction when it comes in contact with biologic fluids [14]. Zirconia phases are classified into three phases, monoclinic, tetragonal and cubic depending on temperature [15,16]. The tetragonal phase is required in dental applications, it can be stabilized by adding other oxides like, (MgO),(Y2O3),(CaO) to prevent transformation to fragile monoclinic phase[17]. Partially stabilized tetragonal zirconia with 3 mol % Y2O3 is considered the material of choice as implant material [18].
The laser-based technique has been widely used in the modification of implant surface roughness instead of other traditional techniques. Since it considered as a fast, more accurate [19], minimum heat affected zone and no need for finishing procedures after processing [20,21]. The process of laser material interaction based on interaction of incident photons with the outer electrons of material constituents, which results in excitation of these electrons and return back to stable state within short period of time. This fact explains that heat generation takes place in very thin superficial layer of substrate material, also explains the cause of fast heating and cooling rates of laser material interactions [22].
In case of ceramic materials, laser material interactions considered more difficult than those of metallic materials. Since, in ceramic materials higher energy required for electrons excitation from valence band. So, short and ultra-short pulsed lasers with high peak power are indicated [22].
The out- come of laser material processing is highly governed by laser power and interaction time [23]. Different physical phenomena occur on material surface once the laser beam strikes which include, reflection, absorption, scattering and transmission. The most required one in laser material processing is absorption [24,25].
The absorption of the laser energy by the material is affected by optical and thermal properties of substrate material, it is also affected by laser parameters including, wavelength, mode of operation and power [26]. Absorption of laser energy cause heat generation on the workpeice subsequently desired effect. Heat dissipation into core material results in heat affected zone which may be present in form of cracks [27,28,29].
In laser material processing, the material can be removed by three different ways, melting, vaporization (both ways are categorized as thermal processing) and chemical degradation. In thermal way, the intensity of absorbed laser beam must be high enough to generate required thermal energy for melting and vaporization of the material. While in a chemical way direct bond break down takes place after absorption of incident laser beam [30].
The aim of this study is to compare the effect of two wavelengths of Nd_YAG laser (1064 and 532) nm using different exposure time, in the modification of zirconia surface roughness.
Materials and Methods
Sample preparation
Zirconia block (incoris tzic sirona) was used for sample preparation. Partially stabilized tetragonal zirconia with 3 mol % Y2O3 pre sintered discs obtained by CAD-CAM technique, polished by using diamond paste of 0.9 μm particle size and its corresponding clothe and grinding or polishing machine. Then the polished discs sintered according to manufacturing instructions to get final experimental samples of dimensions 7.2 mm diameter and thickness respectively.
Absorption spectrum assessment
Post sintering zirconia sample assessed in photo-spectrometer in U.V. visible and IR regions to determine the absorptivity of zirconia for Nd- YAG laser 532 nm.
Laser irradiation
Q-switched Nd-YAG laser (DAESHIN ENTERPRISE) of (1064 and 532) nm wavelengths was used in this study. The samples were divided inti three groups. The first group was irradiated by (1064 nm) Nd-YAG laser by using same parameters (Energy Density and Frequency) except exposure time, as in following Table 1.
Sample no | Energy density (J\cm2) | Frequency (HZ) |
Exposure time (sec) |
---|---|---|---|
1 | 38.22 | 10 | 3 |
2 | 38.22 | 10 | 5 |
3 | 38.22 | 10 | 7 |
Table 1: First group.
The diameter of laser beam used for this group was 5 mm. The second group was irradiated by Nd-YAG laser of (532) nm wavelength. The group of three samples irradiated by using same parameters (Energy density and Frequency) except exposure time, as in following Table 2.
Sample no | Energy density (J\cm2) | Frequency (HZ) |
Exposure time (sec) |
---|---|---|---|
1 | 19.11 | 10 | 3 |
2 | 19.11 | 10 | 5 |
3 | 19.11 | 10 | 7 |
Table 2: Second Group.
The spot size in this experiment was 2.5 mm and the control group, without laser irradiation.
Analysis of surface roughness and topography Surface topography of all samples was assessed by scanning electron microscope (S.E.M.) and surface roughness was assessed by atomic force microscope (AFM). Irradiated samples were prepared for cross sectional S.E.M. They were mounted and sectioned by the diamond disc to be ready for the microscopic assessment.
Results and Discussion
In this study, S.E.M. results reveal that the machined surfaces in both groups are free of micro-cracks. Several previous studies reported surface micro-cracks resulted from irradiation of zirconia surface by Nd -YAG laser (1064) nm (Figures 1-7) [31-33].
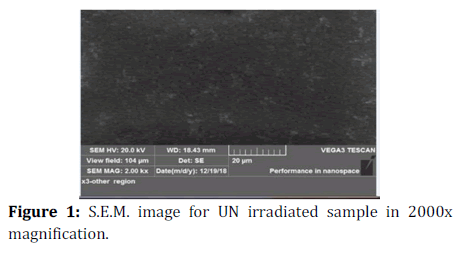
Figure 1. S.E.M. image for UN irradiated sample in 2000 x magnification.
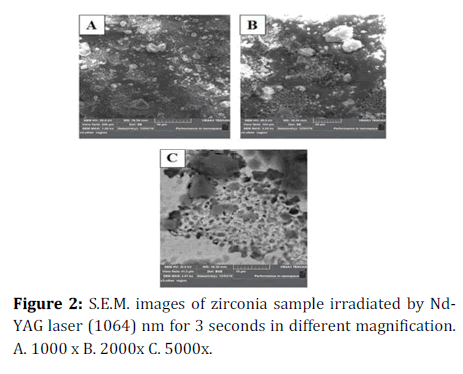
Figure 2. S.E.M. images of zirconia sample irradiated by Nd-YAG laser (1064) nm for 3 seconds in different magnification. A. 1000 x B. 2000 x C. 5000x.
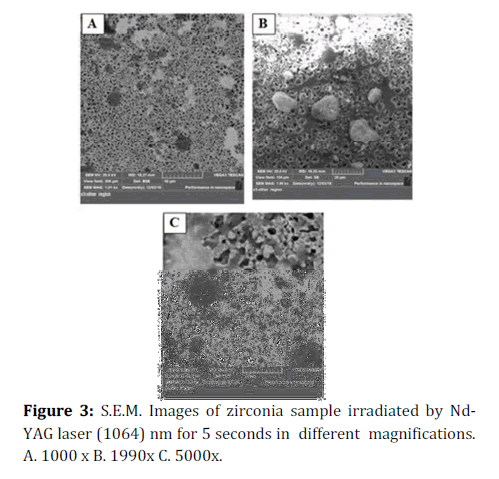
Figure 3. S.E.M. Images of zirconia sample irradiated by Nd-YAG laser (1064) nm for 5 seconds in different magnifications. A. 1000 x B. 1990 x C. 5000x.
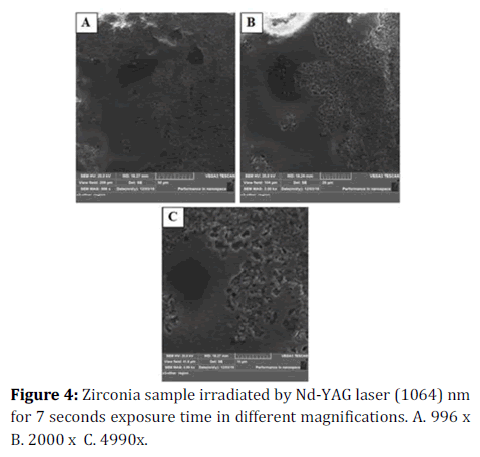
Figure 4. Zirconia sample irradiated by Nd-YAG laser (1064) nm for 7 seconds exposure time in different magnifications. A. 996 x B. 2000 x C. 4990x.
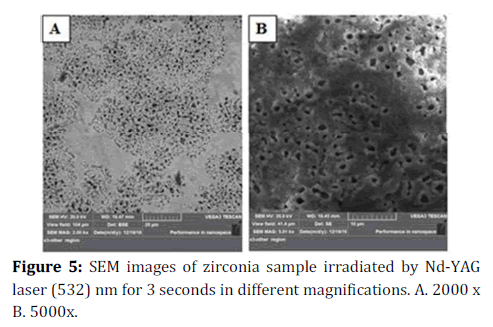
Figure 5. SEM images of zirconia sample irradiated by Nd-YAG laser (532) nm for 3 seconds in different magnifications. A. 2000 x B. 5000x.
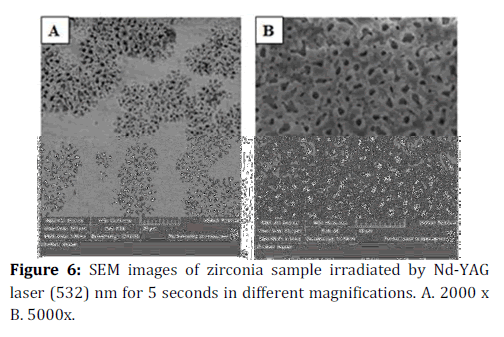
Figure 6. SEM images of zirconia sample irradiated by Nd-YAG laser (532) nm for 5 seconds in different magnifications. A. 2000 x B. 5000x.
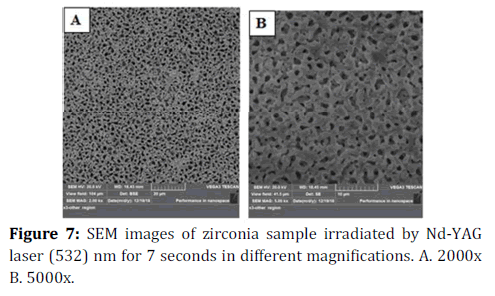
Figure 7. SEM images of zirconia sample irradiated by Nd-YAG laser (532) nm for 7 seconds in different magnifications. A. 2000 x B. 5000x.
Using of laser in material processing is based on conversion of an optical energy into thermal energy after absorption of incident laser beam [34].
During laser material interaction, absorption of incident optical energy by electrons of substrate results in excitation of these electrons, after a specific period of time, these electrons tend to return back to stable state transferring their energy to surrounding atoms this timed is termed as electron – phonon relaxation time [35].
The pulse duration in case of pulsed laser processing has an important role in the final surface changes after laser irradiation. Since the pulse duration and heat affected zone are proportional. Long pulses related to heat dissipation deeply in core material resulting in larger molten material less vaporized [36].
Using lasers with pulse duration of nanosecond considered a preferable option in micromachining of ceramic materials than those of longer pulses because to get better results [37,38] this can be explained by following equation.
Peak power (W) = Laser pulse energy (J) / Pulse duration (s) … (1)[39]
Greater peak power can be obtained with shorter pulses
Importance of using laser with short pulses also can be explained by following equation
(2)
Where ld is the thickness of heat diffusion layer D is diffusion coefficient factor.
tl is pulse duration
From this equation it can be concluded that using long pulses results in heat dissipation into core material and less heat accumulation in absorption layer when compared with short pulsed laser, in which heat accumulation in absorption layer is more [36]. In case of nanosecond pulsed laser the mechanism by which laser beam interacts with substrate is photothermal including melting and vaporizing of material surface [40]. As mentioned above, in this study all irradiated sample of two groups are free of surface microcracks which is due to using pulse duration in nanosecond, heat accumulation in very thin surefacial surface layer raise the temperature to cause melting then vaporization of material.
From S.E.M. images, in Figures 2 and 3 surface porosity of irradiated surface indicates bubble formation in molten material [41].
Presence of scattered spots of molten material represents that the temperature there didn’t exceed melting threshold to reach vaporization temperature [42]. This indicates an inhomogeneous intensity distribution on irradiation area. Cross sectional S.E.M. imaging of the irradiated samples revealed that (Figures 8 and 9).
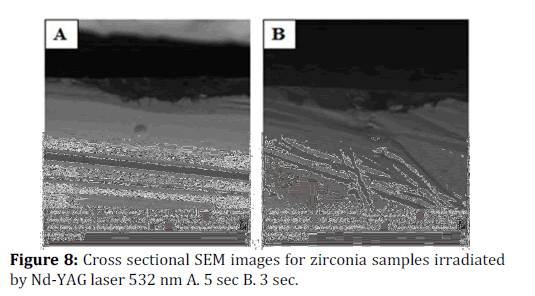
Figure 8. Cross sectional SEM images for zirconia samples irradiated by Nd-YAG laser 532 nm A. 5 sec B. 3 sec.
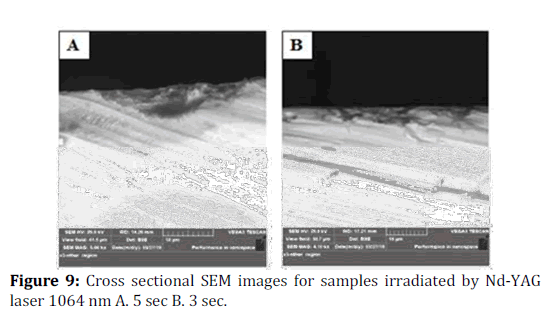
Figure 9. Cross sectional SEM images for samples irradiated by Nd-YAG laser 1064 nm A. 5 sec B. 3 sec.
From the cross sectional imaging, it appears that heat generation on the workpeice is un equal, which caused temperature raising to melting threshold in some areas and to vaporization threshold in others. The same finding where noticed in previous zirconia surface treatment by nanosecond laser [41,43]. S.E.M images of the group irradiated by Nd-YAG laser of (1064) nm wavelength shows presence of scattered surface droplets which considered due to vapor condensation [43].
A.F.M. results revealed increase in the surface roughness directly proportionate to the exposure time. Once the vaporization is initiated at the surface of the material, the continued laser irradiation will cause the liquid–vapor interface to move inside the material. This is accompanied with the evaporative removal of material from the surface above the liquid–vapor interface [44]. Table 3 and Figure 10 shows surface roughnesses of the zirconia samples irradiated by Nd- YAG laser 1064 nm. Table 4 and Figure 11 shows the surface roughness of the zirconia samples irradiated by Nd- YAG laser 532 nm.
Sample no | Exposure time (sec.) |
Surface roughness (nm) |
---|---|---|
1 | Control | 98.5 |
2 | 3 | 401.35 |
3 | 5 | 447.26 |
4 | 7 | 497.5 |
Table 3: Surface roughness’s of the zirconia samples irradiated by Nd- YAG laser 1064 nm.
Sample no | Exposure time (sec) | Surface roughness (nm) |
---|---|---|
1 | 3 | 190.17 |
2 | 5 | 214.67 |
3 | 7 | 444.63 |
Table 4: Surface roughness of the zirconia samples irradiated by Nd- YAG laser 532 nm.
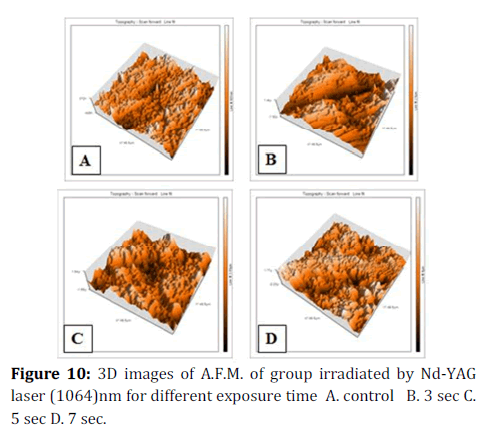
Figure 10. 3D images of A.F.M. of group irradiated by Nd-YAG laser (1064)nm for different exposure time A. control B. 3 sec C. 5 sec D. 7 sec.
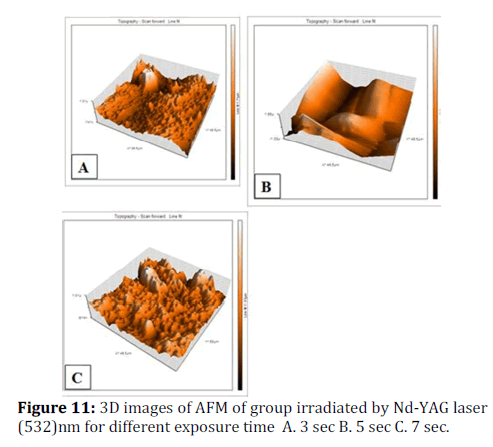
Figure 11. 3D images of AFM of group irradiated by Nd-YAG laser (532)nm for different exposure time A. 3 sec B. 5 sec C. 7 sec.
As mentioned previously, the surface roughness of the zirconia samples irradiated by Nd-YAG laser of a wavelength 532 nm increased inspite of lower energy density used compared with that of 1064 nm. Absorption coefficient of the material plays an important role in determination of the depth of heat generation inside material.
(3)
Where ls is the thickness of the layer the absorbed energy initially penetartes and α is the absorption co efficient [37]. The absorption spectrum of zirconia indicates that zirconia is a good absorber material to (532) nm wavelength (Figure 12).
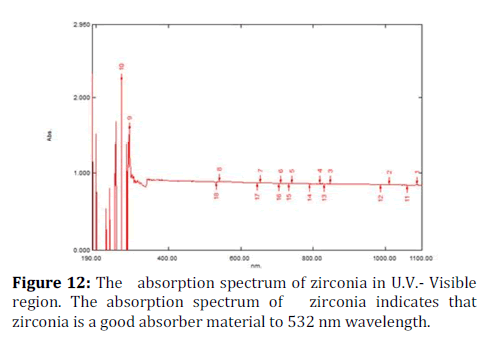
Figure 12. The absorption spectrum of zirconia in U.V.- Visible region. The absorption spectrum of zirconia indicates that zirconia is a good absorber material to 532 nm wavelength.
Conclusion
Q switched Nd-YAG laser of 1064, 532 nm wavelength can be used in zirconia surface roughness modification without surface micro-cracks (as shown in scanning electron microscope imaging).
Atomic force microscope analysis revealed that, surface roughness obtained from irradiation by Nd-YAG laser of 1064 nm wavelength is higher than that obtained from surface irradiation by Nd-YAG laser of 532 nm wavelength.
References
- Powers JM, Sakaguchi RL. In Craig’s Restorative dental materials: Dental Implants. 12th Edn. Elsevier, 2006; 555–569.
- Shah FA, Thomsen P, Palmquist A. Osseointegration and current interpretations of the bone-implant interface. Acta Biomaterialia 2019; 84:1-5.
- Davies JE. Understanding peri-implant endosseous healing. J Dent Edu 2003; 67:932-949.
- Bergemann C, Duske K, Nebe JB, et al. Microstructured zirconia surfaces modulate osteogenic marker genes in human primary osteoblasts. J Mater Sci Mater Med 2015; 26:5350.
- Anselme K. Osteoblast adhesion on biomaterials. Biomater 2000; 21:667-681.
- Drosse I, Volkmer E, Capanna R, et al. Tissue engineering for bone defect healing: an update on a multi-component approach. Injury 2008; 39:9-20.
- Ko HC, Han JS, Bachle M, et al. Initial osteoblast-like cell response to pure titanium and zirconia/alumina ceramics. Dent Mater 2007; 23:1349–1355.
- Lacefield WR. Materials characteristics of uncoated/ceramic-coated implant materials. Adv Dent Res 2007; 13:21-26.
- Albrektsson T, Berglundh T, Lindhe J. Osseointegration: Historic background and current concepts. In: Clinical periodontology and implant dentistry. 4th Edn. Blackwell Munksgaard, Oxford, 2003; 809–820.
- Alla RK, Ginjupalli K, Upadhya N, et al. Surface Roughness of Implants: A Review 2011; 25:112-118.
- Delgado-Ruiz R, Romanos G. Potential causes of titanium particle and ion release in implant dentistry: A systematic review. Int J Mol Sci 2018; 19:3585.
- Depprich R, Ommerborn M, Zipprich H, et al. Behavior of osteoblastic cells cultured on titanium and structured zirconia surfaces. Head Face Med 2008; 8:4–29.
- Hisbergues M, Vendeville S, Vendeville P. Zirconia: Established facts and perspectives for a biomaterial in dental implantology. J Biomed Mater Res B Appl Biomater 2009; 88:519–529.
- Torricelli P, Verne E, Brovarone CV, et al. Biological glass coating on ceramic materials: in vitro evaluation using primary osteoblast cultures from healthy and osteopenic rat bone. Biomater 2001; 22:2535–2543.
- Piconi C, Maccauro G. Zirconia as a ceramic biomaterial. Biomater 1999; 20:1-25.
- Kawai Y, Uo M, Wang Y, et al. Phase transformation of zirconia ceramics by hydrothermal degradation. Dent Mater J 2011; 30:286-292.
- Evans AG, Cannon RM. Toughening of brittle solids by martensitic transformations. Acta Met 1980; 34:761-800.
- https://www.iso.org/standard/62373.html
- Kurella A, Dahotre NB. Review paper: Surface modification for bioimplants: The role of laser surface engineering. J Biomater Appl 2005; 20:5-50.
- Kuar A, Doloi B, Bhattacharyya B. Modeling and analysis of pulsed Nd:YAG laser machining characteristics during micro-drilling of zirconia (ZrO2). Int J Mach Tools Manuf 2006; 46:1301–1310.
- Bagger C, Olsen FO. Pulsed mode laser cutting of sheets for tailored blanks. J Mater Process Technol 2001; 115:131–135.
- Perveen A, Molardi C, Fornaini C. Applications of laser welding in dentistry: A state-of-the-art review. Micromachines 2018; 9:209-.
- Mordike BL. Materials Science and Technology. 1993; 15:111.
- Samant AN, Dahotre NB. Laser machining of structural ceramics a review. J Eur Ceram Soc 2009; 29:969–993.
- Schaaf P. Laser processing of materials. Springer, 2010; 243.
- Bäuerle DW. Laser processing and chemistry. 4th Edn. Springer, 2011.
- Parry JD, Shephard JD, Hand DP, et al. Laser micromachining of zirconia (Y-TZP) ceramics in the picosecond regime and the impact on material strength. Int J Appl Ceram Technol 2011; 8:163–171.
- Parry JP, Shephard JD, Dear FC, et al. Nanosecond-laser post processing of millisecond-laser-machined zirconia(Y-TZP) surfaces. Int J Appl Ceram Technol 2008; 5:249–257.
- Heiroth S, Lippert KT, Wokaun A, et al. Laser ablation characteristics of yttria-doped zirconia in the nano second and fem to second regimes. J Appl Phys 2010; 107:14908.
- Dubey AK, Yadava V. Laser beam machining: A review. Int J Mach Tools Manuf 2008; 48:609–628.
- Paranhos MP, Burnett LH, Magne P. Effect of Nd: YAG laser and CO2 laser treatment on the resin bond strength to zirconia ceramic. Quintessence Int 2011; 42:79–89.
- Akyıl MS, Uzun IH, Bayındır F. Bond strength of resin cement to yttrium stabilized tetragonal zirconia ceramic treated with air abrasion, silica coating and laser radiation. Photomed Laser Surg 2010; 28:801–808.
- Arami S, Tabatabae MH, Namdar SF, et al. Effects of different lasers and particle abrasion on surface characteristics of zirconia ceramics J Dent 2014; 233-241.
- Cavalcanti AN, Pilecki P, Foxton RM, et al. Evaluation of the surface roughness and morphologic features of Y-TZP ceramics after different surface treatments. Photomed Laser Surg 2009; 27:473–479.
- Rihakova L, Chmelickova H. Review article laser micromachining of glass, silicon, and ceramics Adv Mater Sci Eng 2015; 2015:1-6.
- Liu X, Du D, Mourou G. Laser ablation and micromachining with ultrashort laser pulses. J Quantum Electron 1997; 33:1706–1716.
- Karnakis D, Rutterford G, Knowles M, et al. High quality laser milling of ceramics, dielectrics and metals using nanosecond and picosecond lasers in 5th Edn. Photon processing in microelectronics and photonics. Proceedings of SPIEUSA 2006.
- Liu D, Cheng J, Perrie W, et al. Femtosecond laser micro structuring of materials in the NIR and UV regime in Proceedings of the 26th International congress on applications of lasers and electro optics, 2007; 12–18.
- Jonathan R. Lawrence, Waugh D. Laser surface engineering. Woodhead publishing, 2008.
- Allmen M, Blatter A. Laser-beam interactions with materials. Springer, 1995.
- Daniel C, Armstrong BL, Howe JY, et al. Controlled evolution of morphology and microstructure in laser interference-structured zirconia. J Am Ceram Soc 2008; 91:2138–2142,
- Chevalier J, Gremillard L, Virkar AV, et al. The tetragonal-monoclinic transformation in zirconia: lessons learned and future trends. J Am Ceram Soc 2009; 92:1901–1920.
- Heiroth S, Koch J, Lippert T, et al. Laser ablation characteristics of yttria-doped zirconia in the nanosecond and femtosecond regimes. J Appl Phys 2010; 107:14908.
- Dahotre NB, Harimarkar SP. Laser fabrication and machining. Springer, 2008.
Author Info
Sena Raed Muhy and Basima Mohammed Ali Hussein*
Institute of Laser for Postgraduate Studies, University of Baghdad, IraqCitation: Sena Raed Muhy, Basima Mohammed Ali Hussein, Analysis of Nd: YAG Laser (1064 and 532 nm) Interaction with Zirconia Dental Implant after Different Exposure Time, J Res Med Dent Sci, 2019, 7(6): 40-47.
Received: 24-Oct-2019 Accepted: 05-Nov-2019